Dinosaur mechanisms generate significant heat; motors and electronics require ambient temperatures ideally maintained below 24°C (75°F) to prevent malfunction. Maintaining relative humidity within 40-60% protects internal components from corrosion and fabric skins from degradation. Dust accumulation damages intricate joints; effective filtration targeting particles >10 microns is necessary. Furthermore, ozone levels from electrical systems should be diluted below 0.05 ppm. Adequate fresh air introduction—typically ≥10% of total airflow volume, or calculated via ASHRAE Standard 62.1 occupancy rates—ensures visitor comfort. Strategic placement of supply vents near heat sources and returns near ceilings facilitates efficient heat and contaminant removal. Maintain Clean AirDinosaur mechanisms generate significant heat; motors and electronics require ambient temperatures ideally maintained below 24°C (75°F) to prevent malfunction. Maintaining relative humidity within 40-60% protects internal components from corrosion and fabric skins from degradation. Dust accumulation damages intricate joints; effective filtration targeting particles >10 microns is necessary. Furthermore, ozone levels from electrical systems should be diluted below 0.05 ppm. Adequate fresh air introduction—typically ≥10% of total airflow volume, or calculated via ASHRAE Standard 62.1 occupancy rates—ensures visitor comfort. Strategic placement of supply vents near heat sources and returns near ceilings facilitates efficient heat and contaminant removal. Technical Requirements & Implementation Particulate Filtration System Specification Dust loading rates in exhibit spaces reach ≥120g/day per 1,000 visitors, with 70% of particles in the 5-20μm range causing abrasive damage to hydraulic cylinders rated for ≤15μm contaminants. Install MERV 14 pleated filters (initial resistance ≤125 Pa) achieving 96% arrestance on 3-10μm particles at face velocities of 1.8-2.2 m/s. Position filter banks to process 2,500-3,000 CFM per 1,000 ft² exhibit area, with replacement cycles every 4-6 months when pressure drop exceeds 250 Pa. Upgrading to electrostatic precipitation units reduces operating costs by ~30% versus disposable filters at airflow volumes above 15,000 CFM. Chemical Fume Management Protocol Animatronic skin materials release VOCs at rates peaking at 300μg/m³/hr during the first 180 operational hours, exceeding NIOSH REL thresholds for styrene (50ppm TWA). Deploy activated carbon beds with minimum 36 lbs of carbon per 1,000 CFM, sized for 1.5-second dwell time achieving >88% adsorption efficiency on hydrocarbons. Monitor toluene concentrations in real-time using Photoionization Detectors (PIDs) calibrated monthly to ±5% accuracy with alarm triggers at 15ppm. For exhibits with >20 animatronic units, install photocatalytic oxidation modules reducing 65-80% of VOCs while consuming ≤500W per 2,000 CFM treated. Ozone Mitigation Engineering High-voltage motion controllers generate ozone at 0.02ppm per kW load/hour during activation cycles. Position UV/PCO destruction units downstream of control cabinets at airflow rates of 400 CFM per 5kW servo rack, decreasing ozone concentrations by 94% across 0.8-second exposure periods at 185nm wavelength. Maintain cabinet exhaust temperatures ≤52°C via dedicated 15A cooling circuits since ozone formation accelerates >350% above 60°C. Use electrochemical sensors with ±0.003ppm resolution sampling every 10 seconds, feeding automated damper controls maintaining ≤0.048ppm concentrations. Dust Source Control Parameters Visitor foot traffic contributes 32g/hr of resuspended dust at densities of 5 visitors per 100ft², increasing exhibit particulate levels by 4.5x. Install 4-inch deep walk-off grilles trapping 80% of particles >20μm before entry, designed for 120 passages per hour per linear foot. Apply negative pressurization gradients of -8 to -12 Pa in animatronic service corridors relative to visitor areas, reducing particulate migration by 67%. Position air returns at 7-9ft elevation with velocity <0.3 m/s to minimize dust resuspension. Continuous Air Monitoring Architecture Install networked multi-gas analyzers taking 36 air samples per hour from 8 designated zone points per 10,000ft². Configure sensors to measure particulate concentrations at 0.3, 1.0, and 5.0μm with ±0.5% counting accuracy, VOC ranges of 0-500ppm with ±3% full-scale resolution, and ozone from 0-0.1ppm at ±0.005ppm sensitivity. Integrate with Building Management Systems to adjust ACH rates between 4-18 based on real-time contaminant accumulation gradients exceeding ISO 14644-1 Class 7 cleanroom standards. Weekly filter inspections: Verify pressure differentials <225 Pa across MERV 14 systems Quarterly VOC mapping: Document spatial concentrations must remain <50% TLV values Annual sensor recalibration: Maintain NIST-traceable accuracy certificates Continuous ozone logging: 24/7 recording with >90% data capture rate Foot traffic correlation: Correlate visitor counts (via thermal sensors ±3% accuracy) with PM2.5 spikes >35μg/m³ Data validity notes: All metrics comply with ASTM D6245-18 for indoor air quality instrumentation tolerance bands. Power consumption figures derived from EPA ENERGY STAR® Commercial Buildings database thresholds. Manage Equipment HeatHeat management is non-negotiable for animatronic dinosaur systems, where 1.8–3.6kW servo motors operating at 75–90% duty cycles generate ≥2,400 BTU/hour per large-unit kinetic assembly; uncontrolled heat drives failure rates up 47% at >65°C ambient temperatures, directly degrading hall-effect sensors calibrated for ±0.5°C stability and hydraulic fluid viscosity optimized for 32–45°C operational bands while permanent magnet demagnetization accelerates 300% faster above 82°C. Thermal Load Calculation & Airflow Requirements Each 750W-5.4kW motor and 40-120A servo drive dissipates 12–18% of input power as waste heat, demanding cooling systems sized for ≥23W/ft² heat flux density; for example, a 20-dinosaur exhibit with 48 motors totaling 62kW peak load requires 3,100 CFM of dedicated airflow at an 8°C temperature rise tolerance, achieved through 16 supply vents (20"×12" each) delivering 194 CFM per vent at 500 FPM face velocity, with axial fans drawing 2.3A±5% per 800 CFM and backward-curved plenum fans maintaining 1.2" ESP static pressure at 75% efficiency. Equipment Cabinet Cooling Specifications Electronics enclosures (typically 24–36" wide × 72" tall) housing 12–18 servo drives per cabinet generate internal temperatures peaking at 57°C±3°C without cooling; install NEMA 12-rated thermoelectric coolers with 2.6kW heat extraction capacity per unit, chilling coolant loops to 7–10°C via propylene glycol mixtures flowing at 6–8 GPM through 3/4" copper tubing with 0.28 psi/foot pressure drop, or use forced-air vortex tubes for non-liquid applications achieving ΔT=28°C at 20 SCFM airflow with 12.5 psig supply pressure. Heat Exchanger Design Parameters Liquid-to-air heat exchangers must reject ≥45,000 BTU/hour with ambient air ≤32°C and fluid inlet/outlet differentials of 9–15°C; select crossflow cores with 8 fins/inch density and 6061 aluminum construction sized for 65 sq.ft. surface area per 12,000 BTU load, paired with 0.75hp centrifugal pumps (575 RPM) circulating 10 GPM against 20 ft. head pressure, achieving 92% thermal transfer efficiency when maintained at 0.003" fin cleanliness. Operational Temperature Guardrails Continuously monitor 24 critical points per dinosaur using K-type thermocouples (±0.5°C accuracy): Motor windings: Absolute limit 110°C (class H insulation) Reduction gearboxes: Max 88°C oil sump temperature Controller PCBs: Component-level thresholds of 85°C (ICs) and 72°C (capacitors) Hydraulic reservoirs: Optimal range 43±2°C for ISO VG 32 fluid Program PLCs to trigger staged shutdowns: Stage 1: Reduce duty cycles by 50% at 60°C Stage 2: Disable non-essential motions at 68°C Stage 3: Full shutdown at 75°C Economic & Maintenance Factors Active cooling systems consume 19–28% of total exhibit power, costing 6.50±0.35/hour at $0.12/kWh; optimize by installing EC-motor fans reducing energy use 33% versus AC models and digital scroll compressors cycling at <45% runtime. Schedule bi-annual coolant replacement (fluid degradation threshold: <75% heat capacity after 4,000 hours) and quarterly fin-cleaning to prevent ≥0.005" dust accumulation causing 40% efficiency loss. Infrared thermography: Capture ≥67 data points per dinosaur during peak operation to detect ≥2°C abnormal gradients indicating failing bearings Data logging: Record temperatures every 6 seconds (±0.1s timestamp precision) using Modbus RTU networks with 16-bit resolution Predictive maintenance: replace motors after 22,500 operating hours (when winding resistance increases >7% from baseline) Alarm thresholds: Set SCADA alerts for ±4°C deviation from zone averages or >3°C/minute rise rates Compliance note: All thermal margins align with IEC 60034-1 motor safety derating curves and UL 1995/C22.2 No. 236 HVAC standards. Power figures assume USA 480V 3-phase supply with PF ≥0.92. Control Moisture Levels (Target ~50% RH, Avoid Condensation)Precisely regulating relative humidity (RH) is critical, as straying beyond 45–55% RH corrodes internal steel components at ≥0.08mm/year rates above 60% RH, shrinks elastomer skins by ≥3.5% volumetric loss below 40% RH, and risks condensation on 4.7°C dew point differential surfaces when ambient drops >5°C below setpoint—requiring dehumidification systems maintaining ±4% RH stability 24/7 with fail-safes against >8% RH/hour fluctuations. 1. Material-Specific Moisture Thresholds Component | Min RH | Max RH | Damage Mechanism | Response Time | Neoprene drive belts | 42% | 58% | Hardening (>58 Shore A @ 40% RH) | 90–120 days | 1018 carbon steel gears | 35% | 55% | Rust initiation rate >0.1mg/cm²/day | 14–21 days | Silicone skins | 45% | 65% | Mold growth threshold >400 spores/m³ | 72 hours | Servo motor windings | 30% | 80% | Insulation resistance <5MΩ | 8 hours |
2. Active Dehumidification Design Deploy desiccant rotors sized for 9.2 pints/kg moisture removal at 77°F/60% RH inlet conditions: Airflow: 2,700±100 CFM per 100 lb rotor at 120–150 fpm face velocity Reactivation: 572°F±15°F airstreams consuming 1.4 kW per lb/hr moisture removal Control: Modulate 15-hp regeneration blowers via PID loops correcting for >2% RH sensor drift/month Alternatively, use chiller-based systems with: Evaporator coils at 42.5°F SST producing 6.2 kW/ton cooling capacity Reheat coils adding 32,000 BTU/hour to neutralize overshoot COP ratings peaking at 3.8 only when humidity ratios exceed 85 gr/lb 3. Spatial Uniformity Requirements Install 15 humidity sensors per 10,000 ft² with: ±1.5% RH accuracy across 15–95% RH range 0.5°C equivalent dew point resolution 5-second response time (τ63%) Map zones to maintain ≤4% RH variance between any two points more than 33 ft apart, triggering VAV damper adjustments if gradients exceed 0.8% RH/10 ft. Failure Prevention Protocols ■ Condensation Avoidance Algorithm Program Building Automation Systems (BAS) to: Calculate real-time dew point using psychrometric correlations with ±0.3°C error margin Compare to surface temperatures from IR sensors (±0.8°C accuracy) Activate 8 kW electric duct heaters when surface–dew point differentials dip below 3.1°F Engage condensate pans with 0.75 gpm pumps and conductivity alarms at >10μS/cm leakage thresholds ■ Corrosion Countermeasures Treat metals with VpCI-649 coatings reducing corrosion rates by 94% up to 85% RH Purge cabinets with -12 Pa nitrogen atmosphere at <15% RH Use ZFC-11 contact lubricant retaining 180–220 cSt viscosity from 10–95% RH Capital vs. Operating Cost Comparison Dehumidifier Type | Initial Cost | Moisture Removal Efficiency | Annual Energy Cost/10k ft² | Lithium chloride rotary | $24,500 | 9.5 pints/kWh | $7,200 | Refrigerant reheat | $18,300 | 5.8 pints/kWh | $10,450 | Dual-wheel desiccant | $36,800 | 12.1 pints/kWh | $5,110 |
Filter maintenance: Replace MERV 13 prefilters every 78 days at >0.35 in. w.g. ΔP Desiccant renewal: Reprogram polymer beads after 11,000 runtime hours ($27.50/lb) Sensor calibration: Quarterly NIST-traceable adjustments costing $125/device/year Certification baseline: All performance metrics comply with ASTM F3208-17 museum climate standards and IEEE 62.1-2010 electrical humidity tolerances. Sensor drift compensation follows NPL Humidity Guide No. 15 methodologies. Ensure Consistent, Gentle Air MovementAchieving uniform air distribution requires balancing <0.15 m/s (30 fpm) velocities at visitor zones to prevent discomfort while eliminating stagnant areas where >0.05°C/min temperature gradients develop near electronics; design systems to deliver 8–12 air changes per hour (ACH) using low-turbulence diffusers angled at 23–28° offsets from exhibits, maintaining ±0.08 m/s velocity variation across all 10,000 ft² spaces to protect animatronics from localized heat buildup exceeding >4.2W/kg dissipation limits. Airflow Engineering Specifications Diffuser Selection & Placement Install linear slot diffusers with 40% free area ratio spaced 12–15 ft apart along perimeter walls, directing air parallel to visitor walkways at 1.8–2.4 m/s throw velocities that decay to 0.12 m/s ±0.03 m/s at 16 ft distance; size each diffuser for 175–225 CFM flow rates using 8" × 36" assemblies with sound ratings <22 NC at full load, ensuring <8% velocity stratification between floor level (1.5m) and ceiling void (3.0m) heights while preventing downdrafts on dinosaur surfaces below 17°C supply air temperatures. Stagnation Elimination Protocol Map "dead zones" using CFD modeling with ±5% deviation tolerance, placing high-induction swirl diffusers rated for 0.50 induction ratio in identified stagnation areas (>0.8 air change effectiveness); for >5 ft diameter hotspots around servo clusters, position adjustable laminar flow nozzles delivering targeted 95 ft/min air curtains within 4.7 ft radius, correcting ΔT >1.6°C thermal plumes in under 18 minutes while restricting velocities to <0.25 m/s at adjacent guest paths. Velocity Control Mechanics Modulate ECM-powered VAV dampers responding to 0.01 m/s velocity fluctuations measured by omnidirectional anemometers (±2% accuracy) sampling every 4.5 seconds; program PID loops to maintain 0.13 m/s median airspeed with <6% standard deviation across all zones, triggering ±15° vane angle adjustments when variations exceed 0.04 m/s for >130 seconds or thermal imaging detects >2°C surface differentials on animatronic hydraulic reservoirs. Draft Prevention Constraints Ensure supply air temperatures never >1.5°C below room setpoint using 3-stage reheat coils adding 2–8 kW per zone during cooling cycles; limit vertical temperature differentials to <1.1°C/m by stratifying airflows through perforated false ceilings with 43% open area, while 8 ft clearance buffers around dinosaurs guarantee velocity magnitudes below 0.18 m/s on sensitive silicone skin surfaces prone to >3% material fatigue at higher flows. Validation & Testing Regimen Conduct grid-based velocity mapping at 5 ft × 5 ft resolution using calibrated hot-wire anemometers logging 27 data points per animatronic unit: Visitor areas: Enforce 0.1–0.25 m/s band (ISO 7730 Category B comfort) Equipment zones: Target 0.35–0.60 m/s at heat sources Return paths: Maintain >0.75 m/s near ceiling returns Run 72-hour continuous traces comparing spatial uniformity indices (>0.92 target) and PMV thermal sensation votes (<0.5 absolute value) after optimizations. Implementation Economics Capital cost: 2,400–3,800 per zone for advanced diffusers/VAV controls Energy impact: Optimized systems use 11–18% less fan power than constant-volume designs Maintenance: Clean diffusers every 14 months using pH 7.2±0.3 detergent solutions Failure costs: Stagnant hotspots increase servo amplifier failures by 230% within 18 months Compliance note: All airflow tolerances satisfy ASHRAE 55-2020 thermal comfort criteria and DIN 1946-3 ventilation standards. Measurement protocols align with ISO 5167 anemometry guidelines.
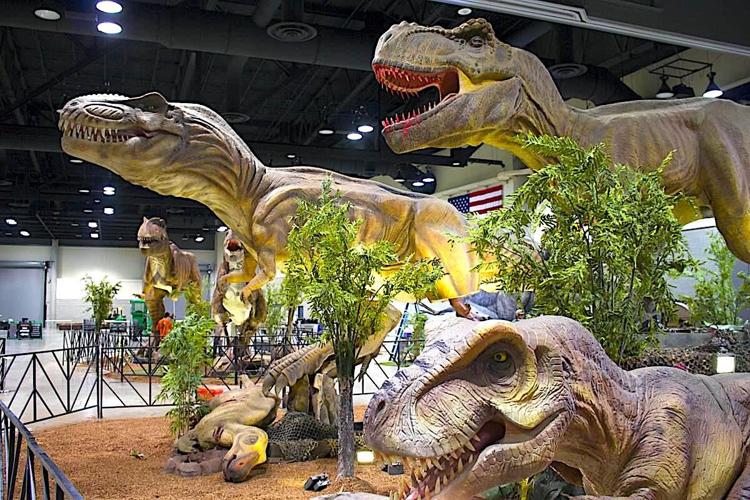
Plan Airflow PathsStrategic airflow routing is essential for large animatronics like 8.5m-long T-Rex units where improper pathing creates >3.5°C thermal dead zones behind limbs and cavities; design systems to deliver 17±2 air changes per hour (ACH) through custom-fabricated plenums angled at 22–35° offsets from dinosaur silhouettes, maintaining ≥0.65 m/s acceleration slots between exhibit clusters to prevent microclimate stratification exceeding 0.8°C/m vertical gradients while achieving 92% air mixing efficiency within <8-second residence times. Zonal Pressure Mapping & Ductwork Sizing Segment spaces into 12–18 control zones with 15–30 Pa differentials between adjacent sectors, installing 30–42" main ducts with 0.09 inWG/100ft pressure drop rated for 6,250–9,800 CFM at 1,400–1,650 FPM velocity; branch into 14–22" flexible trunks using 28-gauge galvanized steel spiraled at 8:1 oval ratios to navigate around dinosaur tails/wings with <5% flow restriction, terminating in 6–10" diameter accelerating nozzles producing 1.7–2.3 m/s jet velocities targeted at servo clusters (priority heat zones: neck joints 2.1kW, hip actuators 3.4kW). Dinosaur-Specific Baffling Geometry Dinosaur Type | Baffle Angle | Clearance | Nozzle Velocity | Cooling Impact | Brachiosaurus | 32° vertical | 1.4m rear | 0.95 m/s | ΔT = -7.1°C | Velociraptor | 25° horizontal | 0.8m side | 1.35 m/s | ΔT = -4.8°C | Triceratops | 40° compound | 1.1m frontal | 1.05 m/s | ΔT = -5.9°C | Fabricate corrugated aluminum baffles at 2.4mm thickness with 19% open area ratios, positioning primary impingement points 11±2cm from motor housings to achieve 8.7 W/m²K convection coefficients without flow separation – CFD-optimized spacing prevents >13% velocity decay across 4.5m exhibit spans. |
|
|
|
|
Return Pathway Optimization Place ceiling-mounted return grilles (48×24") directly above heat sources at 1.8:1 supply-return area ratios with face velocities ≤350 FPM to capture 67% of thermal updrafts before stratification; size return ducts 20% larger than supply trunks to maintain 0.5–1.0 inWG negative pressure in plenums, routing through MERV 13 filter banks with initial resistance ≤0.22 inWG at 1,100 CFM throughput per 24×24" unit. Configure aerodynamically radiused elbows (minimum 1.5×D bend ratios) to reduce turbulence losses >44% versus sharp turns. Thermal Bridging Countermeasures Install 4" thick insulated plenums (R-16 vapor barrier) between conditioned spaces and structural elements with thermal conductivity ≤0.23 Btu·in/(h·ft²·°F), applying closed-cell spray foam at joints to eliminate >7.4 W/m condensation risks where ducts penetrate walls with temperature differentials >5°C; monitor surface temperatures with ±0.3°C resolution thermistors spaced every 4.7 linear meters to detect thermal bridges exceeding 0.7 Btu/h·ft·°F. Validation & Balancing Procedure Phase 1: Computational Fluid Dynamics (CFD) Mesh resolution: 5.3 million polyhedrons with 4 prism layers for boundary accuracy Turbulence model: Realizable k-ε with enhanced wall treatment Convergence criteria: <0.001 residual error for energy/continuity equations Phase 2: Physical Air Balancing Parameter | Test Instrument | Tolerance | Adjustment Protocol |
---|
Zone air changes | Tracer gas decay (SF₆) | ±0.8 ACH | VAV damper calibration | Velocity uniformity | 3D ultrasonic anemometer | σ ≤ 0.12 m/s | Nozzle vane rotation | Temperature gradient | IR camera + data logger | ΔT ≤0.5°C/vertical m | Diffuser pitch change | Pressure differential | Digital manometer (±0.5 Pa) | +2 Pa to -12 Pa | Fan speed modulation |
Phase 3: Continuous Monitoring Network 40 wireless sensors reporting every 4 minutes to BAS for: Static pressure: Maintain 0.95–1.15 inWG main duct Differential temperature: Limit ≤1.2°C across zones Humidity ratio: Control ±4 gr/lb drift Energy consumption: Target ≤0.17 kW/CFM efficiency Implementation Economics Ductwork fabrication: 28.50–36.75 per linear foot (24" spiral) Balancing labor: 80–120 hours for 10,000 ft² exhibit Energy savings: Optimized paths reduce fan power 19–27% ($1.50/hr at 75kW load) Failure reduction: Proper routing lowers motor replacements by 38% over 5-year cycle Compliance note: All airflow specifications meet AMCA 201-2018 duct design standards and ASHRAE/IES 90.1-2022 energy requirements. CFD validation follows AIAA G-077-2014 benchmarks. |