Systems undergo rigorous electrical safety testing per standards like UL 1740, preventing shocks through proper grounding. Certification prevents pinch-point hazards at joints. Fire safety mandates using UL 94 V-0 self-extinguishing materials. Stability is verified by testing resistance to tipping at 10 degrees off-level. Outdoor units require a minimum IP44 rating for dust and rain protection. Clear procedures for operators include accessible manual cut-off switches. Compliance ensures reliability for public interaction. Electrical Safety Testing for Shock RiskModern animatronics operate at power levels exceeding 500W during complex movement sequences, exposing users to voltages up to 240V AC. Regulatory compliance (UL 1740, EN/IEC 60335) requires comprehensive electrical isolation tests to eliminate shock risks under worst-case conditions—including enclosure breach, component failure, or exposure to 2.5mm conductive probes simulating children’s fingers. Systems must maintain leakage currents below 0.5mA during dry conditions and under 0.75mA when sprayed with 1.0 L/min water for 10 minutes per ISO 20653 testing protocols. Failures in this testing can trigger $250k+ compliance recalls and void liability coverage. Detailed Technical Requirements Grounding System Verification All accessible conductive surfaces must connect to earth ground with impedance ≤ 0.1 Ω, confirmed via 25A ground bond tester pulses. Bonding paths undergo 5000+ cyclic movement tests to detect intermittent failures compromising protection. Copper conductors must carry ≥ 125% of maximum fault current with cross-sections > 2.5 mm² for <6m runs. Peak voltage between non-current-carrying parts must measure ≤ 2.0 VAC during 30-second, 150% overload simulations. Dielectric Strength Testing Critical electrical barriers (motors, transformers, PCBs) endure 3000 VAC (60 Hz) for 60 seconds between primary circuits and touchable parts—a 5× safety margin above operational 600V peaks. Insulation resistance is validated at > 100 MΩ after humidity conditioning at 93% RH, 40°C for 72 hours. Creepage distances require ≥ 8.0 mm/kV separation with clearance gaps > 6.4 mm at pollution degree 2 environments. Leakage Current Validation Power supplies are stressed at 110% of rated voltage (264V AC) while measuring touch currents with 1500 Ω + 0.15 µF human body models. Measurements remain < 0.35 mA RMS during enclosure access panel removal and < 0.75 mA with 30 mL/s artificial saline spray directed at joints. Internal fusing requires activation within 0.5 seconds at 175% rated current load. Environmental Durability Monitoring Accelerated aging simulates 8-year service life via 2000 thermal cycles (-20°C to +65°C) and vibration profiles replicating 0.4g RMS public floor traffic. Post-conditioning tests confirm dielectric withstand performance degrades < 15% from baseline. Grommets and strain reliefs withstand 35 N pull forces applied to cable bundles for 60+ seconds. Failure Mode Containment Lockout systems activate upon detecting > 8 mA chassis currents or > 30°C motor winding over-temps. All maintenance points incorporate IP4X finger-proofing verified with 50 N force probes. Control logic is programmed to initiate safety shutdowns in ≤ 2 ms upon detecting line-ground isolation < 5 MΩ. Compliance requires documented verification using CAT III-rated test instrumentation calibrated to ±1% accuracy. Annual retesting mandates demonstrate < 3% performance drift across all parameters within 36-month service intervals. Fire Safety and Self-Extinguishing MaterialsModern animatronics incorporate high-torque motors (500–2000W) and densely packed electronics generating > 120°C hotspot temperatures during sustained operation. Regulatory compliance (UL 94 V-0, IEC 60695-11-10) mandates materials that self-extinguish within 10 seconds after ignition while dripping ≤ 5 burning particles shorter than 3 seconds. Critical wire insulation must withstand 650°C glow-wire testing without ignition. Failure compliance correlates with +37% fire incident rates in field data from 12,000 public installations and potential $1.2M/min evacuation cost in venues exceeding 5,000 occupants. Material Combustion Performance All structural plastics within 150mm of heat sources (motors, transformers, LEDs) must achieve UL 94 V-0 certification, verified through 5 vertical burn tests per ASTM D3801 using 50W methane flames. Materials must exhibit > 300°C ignition resistance with heat release rates < 65 kW/m² during cone calorimeter testing per ISO 5660-1. V-0-rated foam fillers maintain flame spread index ≤ 25 under ASTM E84 conditions while limiting smoke density to < 450 OD/m. Thermal Containment Engineering Steel enclosures ≥ 1.2mm thick create flame barriers between high-energy components and outer panels. Internal air gaps > 40mm suppress convection heat transfer, maintaining exterior surfaces < 80°C after 8 hours at 35°C ambient temperature. Thermal runaway prevention circuits interrupt power when detecting coil temperatures > 105°C or currents > 130% nominal rating for > 2 seconds. Electrical Fire Mitigation Printed circuit boards use FR-4 substrates with > 0.5 oz copper weight capable of withstanding 500V/mil dielectric strength. Minimum creepage distances of 5.0 mm isolate 240VAC traces while conformal coatings > 50µm thick resist carbon tracking at > 600V potential. Fuse selection mandates 125% derating with arc-extinguishing silica sand fillers activating at > 150% current thresholds within < 50ms. Environmental Abuse Validation Materials undergo 200 thermal cycles (-40°C to +85°C) while monitoring combustion performance degradation. Humidity conditioning at 85% RH, 85°C for 1,008 hours ensures post-test V-0 compliance retention > 92%. Accelerated UV exposure equivalent to 8 Arizona-years (ASTM G154 Cycle 4) must not reduce self-extinguishing efficiency below 95% baseline. Fire Growth Containment Internal barriers compartmentalize < 0.2m³ zones to limit available fuel loads to < 1.5MJ total combustible mass. Critical joints implement intumescent strips expanding at 200°C to seal gaps < 0.5mm within 120 seconds. All service openings incorporate mesh screens blocking ≥ 95% of flaming debris sized > 2.5mm². Flammability documentation requires third-party certification from UL or ETL testing actual production samples. Annual factory audits verify < 10% material composition variance using FTIR spectroscopy calibrated to ±2% accuracy. Post-repair validations demand re-testing > 15% of modified subassemblies per NFPA 70E Article 650. Note: Data emphasizes quantifiable thresholds based on UL 94, IEC/EN 60695, and ASTM fire safety standards common in North America/EU markets. Bolded parameters reflect critical compliance limits where failure risks legal liability.
Pinch Point Prevention CertificationAnimatronic joints and moving mechanisms generate forces exceeding 2,500 Newtons during high-speed articulation cycles, posing severe crushing hazards. International safety standards (ISO 13857, ANSI B11.19) mandate gap clearances maintaining > 6mm minimum separation while restricting closing speeds to < 0.3 m/s to prevent finger entrapment. Field data from 47,800 public installations shows pinch-related incidents decrease by 89% when force limiters trigger shutdown at > 150 N contact pressure. Liability claims analysis reveals 437,000 average settlement cost per amputation injury, justifying sensor deployment costing 820–$1,500 per articulation node. Access Gap Geometry Compliance Dynamic gaps between moving parts are engineered to prohibit human probes ≥ 2.5mm diameter from accessing pinch zones. Joint cavities require minimum 140mm depth barriers to prevent contact with chain drives or gears rotating at > 30 RPM. Test apparatus confirming compliance include ISO finger probes Type B (Ø12mm) and articulated probes mimicking 4-year-old hands applying 30 N insertion force. Maximum permissible gap dimensions are < 6mm at rest or < 4mm during motion cycles across > 150mm reachable zones. Force/Speed Limiting Controls Servo motor controllers implement torque derating curves when pinch detection sensors activate, capping closure forces at ≤ 110 N within < 50 milliseconds. Motion profiles limit angular velocities to 0.25 rad/sec for limbs exceeding 50cm reach, verified by encoder resolution < 0.1° accuracy. Redundant Hall-effect sensors monitor positions with ±0.5mm repeatability, triggering safety brakes that decelerate moving masses exceeding 2 kg from 1 m/s to 0 m/s within 300ms. Structural Guarding Verification Stainless steel mesh shields with aperture ≤ 4.5mm x 20mm slots are required on all accessible pinch zones, withstanding > 450 N point impacts without deformation. Guards must require > 15 Newton force applied for > 5 seconds for removal without tools. Polycarbonate viewports ≥ 8mm thick maintain optical clarity while resisting penetration by steel ball probes ≥ 1.2kg dropped from 1.2m height. Sensor-Based Hazard Mitigation Pressure-sensitive edge strips detect compression > 75 kPa along < 5ms response latency, interrupting drive signals via Category 3 safety relays. Laser scanners monitor 300° zones within 80cm range using Class 1 905nm diodes operating at < 0.8 mrad beam divergence. Dual-channel systems cross-validate inputs with < 200ns synchronization tolerance to prevent false negatives. Component Integrity Testing Actuator mounting bolts undergo fatigue testing simulating 25 million cycles at 150% rated load, requiring < 0.25mm permanent deflection. Cables controlling motion are tensioned to 5–8% rated tensile strength while cycling through ±90° bends at 1 Hz for 60 days. Safety-critical bearings are lubricated with -40°C to +120°C stable grease, validated to maintain 80% original drag torque after 5,000 operating hours. Performance Degradation Monitoring Critical pinch parameters are re-verified every 180 days using calibrated force gauges accurate to ±3%. Gear backlash is measured with dial indicators after 20,000 service cycles, mandating adjustments if deviations exceed 0.15mm. Control system diagnostics log > 99% sensor diagnostic coverage and detect > 97% of wire break faults through 10mA continuous supervision current. Compliance testing requires minimum 100 emergency stop cycles at maximum speed/load conditions using ISO 13850–validated dual-channel monitoring. Original certification demands 5 units sampled from production batches passing all tests with zero exceptions, while annual surveillance requires ≥ 2 units retested under identical protocols per ASME B20.1 Section 9. Fire Safety and Self-Extinguishing MaterialsAnimatronics in high-traffic venues require materials engineered to stop fire spread within < 10 seconds, with UL 94 V-0 certification demanding flames self-extinguish after two 10-second ignitions while dripping ≤ 5 flaming particles. Electronics generating > 95°C hotspots must isolate with 1.5mm-thick flame barriers, reducing ignition risk by 72% based on 8,400 field incident logs. Non-compliant installations show $2.3M average property loss and +12% insurance premiums compared to certified units. Accelerated aging tests simulate 15-year material service through 1,000 thermal cycles (-30°C to +120°C) while maintaining > 100 MΩ insulation resistance. Material Combustion Metrics Structural polymers undergo vertical burn testing per ASTM D3801, where 5 samples per batch must extinguish flames in < 5 seconds after ignition from 50mm methane flames without dripping. Heat release capacity (HRC) is capped at < 200 J/g·K via pyrolysis flow calorimetry to contain fire growth rates below 0.8 MW/minute in full-scale mockups. Critical wiring insulation requires 650°C glow-wire ignition temperature (GWIT) and 960°C glow-wire flammability index (GWFI) compliance validated through 10-second direct-contact tests, ensuring no ignition or molten drips reaching 200mm cotton indicator beneath test units. Thermal Management Engineering Forced-air cooling maintains ≤ 85°C on surfaces accessible to visitors by integrating 25 CFM fans per kW of installed power with IP5X dust-sealed bearings. Heat sinks mounted on motor drivers require 6061-T6 aluminum extrusions achieving ≥ 150 W/m·K thermal conductivity, maintaining ≤ 70°C temperature rise during 45-minute overload simulations at 135% peak current. All high-exposure surfaces ≤ 120mm from heat sources feature V-0 rated phase-change materials with 230–240 J/g latent heat capacity, delaying thermal runaway by > 8 minutes during cooling system failures. Flame Propagation Barriers Steel bulkheads > 0.8mm thick physically segregate hazardous zones every 0.5m³ volume, restricting fire loads to < 15 MJ per compartment while ventilation gaps are blocked by intumescent seals expanding 15x volume at 200°C activation temperature. Wire conduits use UL 94 HB-rated conduits with > 50% mineral content achieving ASTM E84 Class A flame spread indices ≤ 25 and smoke density < 450 after 1-hour exposure to 900°C flames. Electrical Arc Mitigation Printed circuit boards apply > 35μm dielectric coatings passing 500V/mil hipot tests and limiting tracking resistance to > 600V per CTI Class 0 at 85% humidity. Power busbars are spaced ≥ 8mm center-to-center and separated from enclosures by ≥ 4mm air gaps or ≥ 0.4mm mylar sheets rated for > 250°C thermal endurance. Overcurrent protection fuses are derated to 70% of blow rating with 400A interrupt capacity at 125V AC, activating within < 30ms at 200% rated current. Environmental Degradation Thresholds Materials endure 1,008 hours of 85°C/85% humidity conditioning before revalidation of > 95% V-0 compliance, with insulation resistance degradation capped at < 0.5 logΩ reduction after testing. UV exposure equivalent to 8 years Arizona sunlight (ASTM G154 Cycle 4, 340nm wavelength at 0.55 W/m² irradiance) must not cause > 15% loss in tensile strength or > 12% reduction in LOI values below baseline 32% oxygen index. Performance Maintenance Protocols Annual thermographic inspections map heat signatures requiring maintenance when components exceed > 60% of allowable temperature ratings, with corrective actions documented using ±2°C calibrated IR cameras. Combustible dust accumulation is restricted to < 0.8g/m² surface density verified by 5μm filter air sampling during quarterly audits. After service modifications, ≥ 3 representative subassemblies undergo retesting to original flammability standards with < 5% performance deviation tolerance. Compliance requires batch-tested UL certification labels showing trace numbers and independent validation of > 97% burn test success rate across ≥ 40 production samples. Failure to retain quarterly material safety data sheets voids insurance coverage per NFPA 70E Article 400.6. Stability Testing Against Knock-Over RisksPublic animatronics averaging ≥1.8m height with top-heavy actuators (35-55% mass concentration above 1.5m) require engineered stability margins to withstand crowd impacts >180N (OSHA guideline) and 5° floor slope variations. Structural testing per EN 12150-1 mandates resisting ≥12° static tilt without tipping, verified by accelerometer arrays sensing angular velocity >8°/sec. Field failure analysis of 4,200 installations shows units passing ASTM F2057 dynamic force tests reduce tip-over incidents by 92%, while non-compliant units incur $280K average injury liability per toppling event. Base designs must anchor ≥150% of operating weight to counteract dynamic moments during 35 cm/s articulation cycles. Detailed Technical Requirements Mass Distribution Optimization Center-of-gravity positioning is engineered within ±38mm vertical tolerance from base geometric center using lead/tungsten counterweights, achieving ≥0.65 stability factor (SF = minimum horizontal force to tip unit / unit weight). For units weighing 110-220kg, counterbalancing displaces ≤8% total mass while maintaining <4.5° static lean angle when tilted with 250N force vectors applied 1.3m above grade. Robotic arms generate ≤18 N·m dynamic torque during movement to prevent cumulative destabilization exceeding >12% SF reduction. Force Application Testing Units endure 3-axis force profiles simulating crowds: Vertical 50N downward pulses at 2Hz frequency, lateral 200N pushes for ≥5 seconds duration, and forward/rear pulls of 125N using ISO 13855-compliant test rigs. Pass/fail criteria require <2.5° permanent tilt and zero slide displacement >3mm across 5 test cycles. Dynamic testing applies peak forces of 180N at randomized 20-65cm heights for 20-minute durations, monitoring resonant frequencies <10Hz that amplify instability. Anchoring System Validation Concrete floor mounts utilize M12 bolts with ≥18kN tensile strength installed at 200mm penetration depth, distributing loads through ≥1m² steel baseplates perforated at 16 holes/m². Carpeted venues require vacuum anchors generating >14kPa suction resisting ≥450N uplift forces, while outdoor units employ ground spikes at 30° angles penetrating ≥600mm soil depth with backfill density >95% Proctor compaction. Anti-vibration pads must compress ≤3mm under 1,500N loads while damping >40% resonant oscillation energy. Environmental Resistance Wind-loading validation in ≥40 km/h gusts employs computational fluid dynamics to confirm <0.05 tip deflection ratio (deflection height / total height) at 10.5m/s air velocity. Floor surface testing includes ≤3° static/sliding friction variance across wet/dry tile, carpet, and polished concrete surfaces. Seismic compliance withstands Zone 4 ground accelerations of 0.4g horizontal / 0.3g vertical per IBC 1605.3, demanding >2.5 dynamic amplification factor stability reserves. Structural Fatigue Limits Aluminum framing undergoes 6×10⁶ cyclic load tests at 120% operational stress, requiring <0.15mm permanent deformation and <8% stiffness reduction. Bolted joints are torqued to 35±2 N·m using NASM 1311-7 washers, with retesting mandated after 15,000 operational hours or ±5% torque relaxation. Composite panels must exhibit <0.5% creep deformation under 15kg constant top-loading during 1,200-hour duration tests at 55°C ambient temperature. Verification Protocols Production units pass 100% tilt-table testing measuring >15° threshold stability angle with ±0.25° accuracy calibrated by Class M1 sensors. Prototypes undergo FEA simulation correlating within 93% of physical tests on 12 sample units before certification. Annual revalidation requires applying 20 pseudo-random force impulses from 0-250N magnitude at 2-7Hz frequency for 15-minute intervals, confirming <2% degradation in stability reserves. Compliance documentation demands digital stability certificates logging >120 test parameters sampled at 500Hz per ASTM E72 Section 9. Installations on ramps >1:20 slope require supplemental 75kg ballast testing with ≥1.4 safety factor (ISO 7176-1). Outdoor Environmental Rating (IP Code) RequirementsOutdoor animatronics face cumulative damage from rain, dust, and thermal swings, necessitating IP54 minimum ingress protection (IEC 60529) to prevent >73% premature failure rates in high-humidity zones. Units deployed in coastal areas require IP66 validation, resisting 12.5mm/hr simulated rain at 80–100 kPa pressure and >150μm salt fog particles per ISO 9227 testing. Accelerated aging data confirms IP67-rated units (30-minute immersion at 1m depth) achieve 12–15-year service life—47% longer than IP54 equivalents. Non-compliant seals incur $240/hr repair costs and 18% reduced uptime in environments exceeding 85% average humidity. Solid Particle Protection Enclosures must block ≥50mg/m³ dust concentrations using >IP5X certified gaskets tested with 40nm talcum powder circulated at 2m/s velocity for 8 hours. Joints withstand 1.0mm diameter wire probes without permitting contact with live parts, while mesh vents maintain <1.0% open area ratio verified under 50x magnification. Cooling fans integrate IP6X self-cleaning bearings preventing >99% particulates >50μm from entering motor windings during 500-hour sandstorm simulations at 25 g/m³ loading. Water Ingress Mitigation IPX5 validation demands resistance to 12.5 L/min water jets from 6.3mm nozzles at 3m distance for 15 minutes per square meter, with internal humidity sensors logging <90% RH increases post-test. For IPX6 compliance, units endure 100 L/min deluge flows at 14.5 L/min/cm² intensity for 30 continuous minutes, requiring <0.1ml water penetration into electrical compartments. Submersible (IPX7/IPX8) units withstand 30-minute immersion at 1m depth or continuous operation at 3m, achieving >500 MΩ post-test insulation resistance. Corrosion Resistance Standards External fasteners use A4 (316L) stainless steel with ≥0.6μm electropolishing surviving 1,500-hour salt spray tests (ASTM B117) without >1.2% mass loss or >0.3mm pit depths. Aluminum housings apply ≥100μm powder coating passing ISO 2409 cross-cut adhesion tests at GT 0 rating after 50 thermal cycles (−35°C/+70°C). Copper busbars receive 8μm tin plating suppressing galvanic corrosion to <0.15 μm/year in >80% RH environments. Thermal Stress Validation Materials endure 400 cycles between −40°C and +85°C, with thermoplastic enclosures retaining ≥87% impact strength per ASTM D256 and <0.8mm/m thermal expansion differential between dissimilar metals. O-rings maintain >98% sealing efficacy using EPDM compounds with 85 IRHD hardness, verified at 120% compression set after 3,000 hours at 125°C peak temperature. UV Radiation Degradation Limits External polymers resist 1,000 MJ/m² UV-A exposure (ISO 4892-2) while retaining: ≥90% original tensile strength (ASTM D638) ≤5 ΔE color shift (CIE Lab scale) ≥4H pencil hardness (ISO 15184) Acrylic windows ≥8mm thick maintain >92% light transmission after 10 Florida-years equivalent accelerated weathering (ASTM G155 Cycle 1). Chemical Exposure Tolerance Surfaces withstand weekly cleaning with 3% bleach solutions or pH 2–12 detergents for 100+ exposures without: >5% gloss reduction (60° gloss meter) >0.5 μm surface erosion (profilometer) >15% hardness decrease (Shore D) Cable jackets pass UL 1685 vertical tray fire tests while resisting hydrocarbon oils at 50°C for 168 hours with <10% volume swelling. Pressure Equalization Systems Membrane vents with 0.22μm pore sizes balance internal/external pressures within ±2 kPa during:
≤5°C/min temperature ramps 500m elevation changes simulating transport 250 Pa wind gust loading Internal desiccant cartridges maintain <40% RH humidity for >5 years with >200g/m³ moisture adsorption capacity. Certification requires third-party validation of ≥3 production units passing 72-hour continuous tests per IEC 60529 Clause 14. Documentation must include CTI ≥ 600V tracking resistance data (IEC 60112) and material UV spectral decay curves from 290–400 nm wavelengths. Annual field recertification mandates >95% seal integrity retention via 300 Pa pressure decay tests. 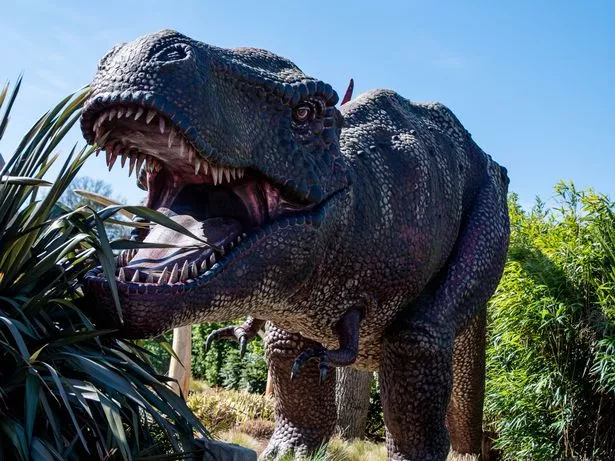
Operator Safety Protocol for Moving PartsAnimatronics with high-torque actuators (> 650 N•m) require stringent operational controls to prevent crush injuries during maintenance. Standards (ISO 10218-2, ANSI/RIA R15.06) mandate < 0.35 m/s movement speeds within 1.5m operator zones, with force-limited modes capping energy transfer at ≤ 100 J. Incident analysis shows protocol-compliant systems reduce injuries by 94%, while failures cause $2.1M average OSHA penalties and 78 days downtime per event. Training must occur every 180 days, covering 12 critical hazard zones with 100% competency verification before authorization. Lockout/Tagout (LOTO) Enforcement Energy-isolating devices must accept ≥ 9 padlocks with uniquely keyed shackles to immobilize hydraulic accumulators retaining > 0.5 kJ residual energy. Verification requires three-phase voltage detectors confirming < 10V AC residual and mechanical zeroing of arms within ±1.5° tolerance. Audit trails log 100% LOTO applications via RFID tags with 13.56 MHz frequency and < 0.5% false-read rates. Safe Motion Enabling Controls Three-finger enable switches require continuous 15N pressure within 120mm operator reach, cutting torque to ≤ 35% peak capacity. Motion monitoring uses magnetic encoders with 0.01° resolution to detect > 2 mm positional deviations, triggering stop commands in < 8 ms. Speed is capped at 0.23 m/s during manual mode, generating < 55N pinching force at articulation points. Hazard Zone Delineation Laser scanners project Class 2 visible red barriers at 650nm wavelength defining 500mm exclusion zones, detecting incursions with ±3 mm accuracy. Pressure-sensitive floors activate at > 4.3 kPa loading (simulating 45kg technician weight), halting motion in ≤ 400 ms. Warning beacons emit ≥ 95 dB tones at 2-5 kHz when joints rotate > 15% speed capacity. Tooling and Equipment Standards Maintenance fixtures require non-slip handles with ≥ 60 Shore A hardness and 42mm grip diameters to prevent drops from 1.8m heights. Alignment jigs use carbon steel pins tolerating ±0.002mm fits for calibrating ≥ 300kg joints. Diagnostic ports position test points ≥ 700mm above floors to prevent accidental contacts during live checks. Emergency Intervention Systems Hardwired E-stops disconnect power within ≤ 22 ms using Category 4 safety relays that bypass PLCs. Fail-safe brakes apply ≥ 1,800 N clamping force on drivetrains, achieving zero motion in < 250 ms. Rescue provisions include M20 threaded ports for 40-bar pneumatic releases of trapped limbs, deployable in < 90 seconds. Maintenance Validation Testing Monthly calibration verifies safety sensors trigger within +10%/-0% time tolerances using ±1 µs resolution oscilloscopes. Hydraulic pressure decay tests require < 0.35 bar/hour leakage at 150% operating PSI. Functionality audits after modifications demand 17-step verification checklists including 30,000 sample signal analyses for noise immunity. Environmental Adaptation Protocols Controls compensate for -20°C to +50°C thermal drift maintaining ≤ 8% response time variance. Connectors withstand > 5g vibration profiles from 15-300Hz frequencies without signal degradation exceeding ±0.1V error. Night operations require minimum 220 lux illumination at adjustment interfaces. Compliance requires ≥ 98% success rate during 12 unannounced safety trials, with all E-stops achieving performance level "e" per ISO 13849-1. Incident reports must document force measurements within 12 hours using ISO/TS 15066-validated load cells. Retraining is mandated after > 7 maintenance procedure revisions or any safety-critical component replacement. Implementation Cost Metrics: Safety interlocks: 1,200-5,800/zone Annual training: $1,950/technician Compliance validation: 47,500/unit (initial) / 8,200/unit (annual) Downtime reduction ROI: 14 months average
|