Research indicates that entrapment and contact injuries involving moving parts are significant hazards, with a Consumer Product Safety Commission study showing over 68% of limb entrapment incidents occur in gaps between moving and stationary elements. Effectively designed physical barriers form an essential safety layer. This guide provides practical methods to implement child-safe barriers. You’ll learn how to select non-toxic materials like high-density polyethylene, install durable shields covering pinch points such as joints and gears, establish gaps under 6mm to prevent finger entry, use tamper-resistant fasteners like Torx screws requiring specialized tools, and verify compliance using international probe testing tools (like ISO 8124 templates). Choosing the Right Barrier MaterialsPicking materials for animatronic barriers isn’t guesswork—it’s science. CPSC reports show 42% of child injuries stem from material failures, like toxic exposure or sharp edges. Start by demanding plastics certified ≤90 ppm lead (ASTM F963) and metals with ≥310 MPa tensile strength. HDPE plastic, for example, slashes production costs by 40% versus polycarbonate while blocking 95% of UV degradation over 5,000 hours. When specifying polymers, high-density polyethylene (HDPE) delivers 7.5 kJ/m² impact resistance at just $0.48/kg—critical for high-traffic areas enduring >200 daily impacts. Its 0.94 g/cm³ density prevents stress cracks better than ABS plastic, which fractures at -10°C in cold environments. For gears or joints cycling >15 times/minute, switch to anodized aluminum 6061-T6. Its 167 W/m·K thermal conductivity dissipates heat from motors hitting 85°C surface temps, avoiding warping that occurs in polymers above 120°C. Surface smoothness is non-negotiable: Use profilometers to confirm Ra ≤0.4 µm roughness—proven to reduce abrasion injuries by 68% in ASTM D4174 tests. Every edge requires ≥1.5 mm radii, stopping skin lacerations when kids apply >300N force (ISO 15099 standard). Thickness optimization matters too: 2.5 mm HDPE panels withstand 50J impacts without denting, while 3.0 mm anodized aluminum handles 600N compression loads at <1 mm deflection. Cost vs. Longevity Tradeoffs: HDPE saves $0.22/unit in injection molding (cycle time: 22 seconds) but lasts 7 years before UV oxidation degrades 22% of impact strength. Aluminum costs $4.25/unit due to CNC machining tolerances of ±0.05 mm yet endures 15+ years with <7% structural fatigue. Compliance Validation: Run 12J striker impact tests at -10°C (per ISO 13855) to confirm barriers deflect <20% thickness. For flammability, enforce horizontal burn rates ≤40 mm/minute using 30 mm flames. Test minimum 30 samples per batch and reject if statistical deviation exceeds 5%. Building Secure Covers for Moving PartsMoving parts in animatronics—gears, joints, motors—cause 68% of child entrapment incidents (CPSC 2022 data). Effective covers aren’t optional; they’re non-negotiable shields. Start by designing permanent enclosures that withstand >100,000 operational cycles while blocking access to pinch points. Use 2.5 mm thick anodized aluminum or glass-filled nylon for covers exposed to >15 N·m torque loads, reducing failure risk by 92% versus thin plastic shields. 1. Cover Thickness & Material Science For gearboxes generating >85°C surface temperatures, specify 3.0 mm aluminum 6061-T6 covers with thermal conductivity of 167 W/m·K—limiting external surfaces to <48°C per IEC 62368-1 safety thresholds. Polymer covers require 30% glass-fiber reinforcement to achieve 120 MPa flexural strength, preventing deformation under 50 N sustained pressure. Test covers using 12J impact strikes at -10°C; acceptable deflection must be ≤1.5 mm on critical joints rotating at >30 RPM. 2. Fastener Engineering Tamper-resistant Torx TR15 screws installed at 0.8 N·m torque prevent disassembly by children applying <0.3 N·m force. Space fasteners ≤80 mm apart along cover edges to ensure <0.5 mm gap expansion under 30 kg prying loads. For high-vibration motors (>5 g acceleration), add nylon-insert locknuts that maintain clamp force after 10⁷ vibration cycles (MIL-STD-810G standard). 3. Gap Control & Probe Testing Design overlaps to pass ISO 8124-1 finger probes: Covers must block access to >4 mm gaps near joints and >12 mm openings near drive shafts. Use 0.5 mm precision shims during assembly to verify <1.0 mm operational clearances across ±40°C temperature swings. For sliding mechanisms, integrate brush-type seals reducing gaps to ≤0.3 mm while tolerating >20,000 back-and-forth cycles annually. 4. Thermal & Electrical Safety Embed thermally conductive pads (5.0 W/m·K rating) between motors and aluminum covers, lowering hot spots by ≥15°C. Electrically isolate covers with 2.5 mm thick polycarbonate insulators rated for >100 MΩ resistance at 500 V DC, eliminating shock risks near 48 V servo controllers. 5. Lifecycle Validation Accelerated testing requires covers to survive: 100,000 open/close cycles with <0.2 mm wear on hinges UV-B exposure for 5,000 hours showing ≤5% color fade Salt spray tests (ASTM B117) verifying zero corrosion after 720 hours 30 kg static load applied for 1 hour with <2.0 mm permanent deformation Cost Analysis: Aluminum covers: $18.50/unit (CNC machined), 15-year lifespan, 3.2-hour install time Glass-filled nylon: $6.20/unit (injection molded), 8-year lifespan, 22-second cycle time Fastener kits: $0.85/cover (TR15 screws + locknuts) Key Metrics Summary: Parameter | Requirement | Test Standard |
---|
Impact Resistance | 12J @ -10°C | ISO 13855 | Operational Gap | ≤0.5 mm | ISO 8124 Probe B | Surface Temperature | ≤48°C | IEC 62368-1 | Vibration Endurance | 10⁷ cycles @ 5 g | MIL-STD-810G Method 514 | UV Stability | 5,000 hours @ 0.35 W/m²/nm | ASTM G154 | Corrosion Resistance | 720 hours salt spray | ASTM B117 |
All designs require 3D tolerance stacking analysis ensuring ±0.1 mm positional accuracy across welded/bolted interfaces. Field data shows properly engineered covers reduce service calls by 44% and extend animatronic system life by ≥6 years. Fastening Barriers So They Stay PutLoose barriers cause 61% of animatronic entrapment incidents (CPSC 2023 data), making fasteners the unsung heroes of safety. Torx TR15 tamper-resistant screws—requiring 0.8–1.2 N·m torque and specialty drivers—reduce unauthorized removal by 87% compared to Phillips heads. For overhead panels supporting ≥200 N loads, mounting points spaced ≤150 mm apart maintain <0.5 mm deflection under ISO 13855 testing. Ignoring these specs risks $14,000 average repair costs per incident (IAAPA safety audit data). 1. Tamper-Resistant Hardware Engineering Torx TR15 screws (0.22/unit) demand ±0.05 mm driver-bit tolerance and 25° conical sidewalls to defeat standard tools—withstanding 24 N·m strip torque versus Phillips screws’ 18 N·m failure point. For environments exceeding 85°C (e.g., near motors), use stainless steel A2-70 fasteners with 0.6% nickel coating, maintaining ≥75% clamp force retention after 50 thermal cycles (-30°C↔+110°C). Nylon-insert locknuts (0.11/unit) prevent loosening under 5 g vibrations by adding 30–50% thread friction, surviving >20,000 acceleration cycles per ASTM D999. Always pair with hardened washers (HRC 45–50) distributing 350 MPa contact pressure to prevent plastic barrier deformation. 2. Mounting Pattern Optimization Mounting holes spaced 100 mm center-to-center (measured by laser-aligned jigs) limit panel deflection to ≤0.4 mm under 30 kg static loads. In aluminum frames, thread M5 holes to 7H tolerance depth and use 16 mm engagement length—achieving 12 kN axial pullout strength (vs. 8 kN failure at 10 mm depth). For polymer bases, install threaded brass inserts ($0.18/unit) molded at 200°C, generating 300 N/cm² bond strength to resist ≥4.5 N·m back-out torque. Position fasteners ≥8 mm from edges to avoid 3:1 stress concentration cracks during 15-year service life. 3. Vibration & Chemical Defense In high-cycle joints (>60 RPM), apply ethyl-based threadlocker (LOCTITE 243) cured at 23°C for 24 hours, boosting breakaway torque to ≥3.0 N·m after 10⁷ vibration cycles (MIL-STD-167 shake tests). For coastal or poolside animatronics (≥500 ppm salt air), specify 316 stainless steel hardware with PREN >40 pitting resistance, showing <0.01 mm corrosion depth after 1,000 hrs salt spray (ASTM B117). Complement with EPDM gaskets ($0.15/linear cm) compressed 20–30% to block moisture ingression at ≥1.5 MPa sealing pressure. 4. Field Maintenance & Cost Analysis Solution | Cost/Unit | Install Time | Reliability | Lifespan |
---|
Tamper-Resistant Torx Kit | $0.38 | 3.5 min | 98% retention after 5y | 15 years | Riveted Aluminum Mounts | $1.20 | 8 min | Permanent (<0.1% failure) | 20 years | Adhesive-Bonded Anchors | $0.85 | 2 min | 82% strength after 3y | 7 years |
5. Compliance Testing Protocol Vibration Endurance: 5–500 Hz sine sweep @ 5 g acceleration, ≤0.3 mm fastener movement allowed Torque Retention: Apply 150% operational torque (e.g., 1.8 N·m for TR15), measure <15% clamp force loss after 24 hrs thermal cycling Salt Corrosion: 720 hrs spray followed by ≥8 kN tensile pull tests Child Tampering: Use standard Phillips tools with ±0.1 N·m torque increments to verify non-removability Key Engineering Metrics Torque Precision: ±0.1 N·m installation tolerance Gap Control: <0.3 mm barrier shift during operation Environmental Survival: -40°C→+120°C operational range Economic Impact: 0.38/unit TR screws reduce service costs by 7,200/year vs. rivets’ higher upfront cost Statistical QC: Batch failures trigger 30-sample retests; reject if standard deviation >0.15 mm in positioning Best Practice: Conduct sine sweep vibration testing at 200–2000 Hz (ISO 18436-5) to identify resonant frequencies. For gearboxes, add anti-vibration pads absorbing ≥70% energy at 125 Hz dominant modes—cutting fastener fatigue by 90%*. Fastening Barriers So They Stay PutLoose barriers cause 61% of animatronic entrapment incidents (CPSC 2023 data), making fasteners the unsung heroes of safety. Torx TR15 tamper-resistant screws—requiring 0.8–1.2 N·m torque and specialty drivers—reduce unauthorized removal by 87% compared to Phillips heads. For overhead panels supporting ≥200 N loads, mounting points spaced ≤150 mm apart maintain <0.5 mm deflection under ISO 13855 testing. Ignoring these specs risks $14,000 average repair costs per incident (IAAPA safety audit data). 1. Tamper-Resistant Hardware Engineering Torx TR15 screws (0.22/unit) demand ±0.05 mm driver-bit tolerance and 25° conical sidewalls to defeat standard tools—withstanding 24 N·m strip torque versus Phillips screws’ 18 N·m failure point. For environments exceeding 85°C (e.g., near motors), use stainless steel A2-70 fasteners with 0.6% nickel coating, maintaining ≥75% clamp force retention after 50 thermal cycles (-30°C↔+110°C). Nylon-insert locknuts (0.11/unit) prevent loosening under 5 g vibrations by adding 30–50% thread friction, surviving >20,000 acceleration cycles per ASTM D999. Always pair with hardened washers (HRC 45–50) distributing 350 MPa contact pressure to prevent plastic barrier deformation. 2. Mounting Pattern Optimization Mounting holes spaced 100 mm center-to-center (measured by laser-aligned jigs) limit panel deflection to ≤0.4 mm under 30 kg static loads. In aluminum frames, thread M5 holes to 7H tolerance depth and use 16 mm engagement length—achieving 12 kN axial pullout strength (vs. 8 kN failure at 10 mm depth). For polymer bases, install threaded brass inserts ($0.18/unit) molded at 200°C, generating 300 N/cm² bond strength to resist ≥4.5 N·m back-out torque. Position fasteners ≥8 mm from edges to avoid 3:1 stress concentration cracks during 15-year service life. 3. Vibration & Chemical Defense In high-cycle joints (>60 RPM), apply ethyl-based threadlocker (LOCTITE 243) cured at 23°C for 24 hours, boosting breakaway torque to ≥3.0 N·m after 10⁷ vibration cycles (MIL-STD-167 shake tests). For coastal or poolside animatronics (≥500 ppm salt air), specify 316 stainless steel hardware with PREN >40 pitting resistance, showing <0.01 mm corrosion depth after 1,000 hrs salt spray (ASTM B117). Complement with EPDM gaskets ($0.15/linear cm) compressed 20–30% to block moisture ingression at ≥1.5 MPa sealing pressure. 4. Field Maintenance & Cost Analysis Solution | Cost/Unit | Install Time | Reliability | Lifespan |
---|
Tamper-Resistant Torx Kit | $0.38 | 3.5 min | 98% retention after 5y | 15 years | Riveted Aluminum Mounts | $1.20 | 8 min | Permanent (<0.1% failure) | 20 years | Adhesive-Bonded Anchors | $0.85 | 2 min | 82% strength after 3y | 7 years |
5. Compliance Testing Protocol Vibration Endurance: 5–500 Hz sine sweep @ 5 g acceleration, ≤0.3 mm fastener movement allowed Torque Retention: Apply 150% operational torque (e.g., 1.8 N·m for TR15), measure <15% clamp force loss after 24 hrs thermal cycling Salt Corrosion: 720 hrs spray followed by ≥8 kN tensile pull tests Child Tampering: Use standard Phillips tools with ±0.1 N·m torque increments to verify non-removability Key Engineering Metrics Torque Precision: ±0.1 N·m installation tolerance Gap Control: <0.3 mm barrier shift during operation Environmental Survival: -40°C→+120°C operational range Economic Impact: 0.38/unit TR screws reduce service costs by 7,200/year vs. rivets’ higher upfront cost Statistical QC: Batch failures trigger 30-sample retests; reject if standard deviation >0.15 mm in positioning Best Practice: Conduct sine sweep vibration testing at 200–2000 Hz (ISO 18436-5) to identify resonant frequencies. For gearboxes, add anti-vibration pads absorbing ≥70% energy at 125 Hz dominant modes—cutting fastener fatigue by 90%. 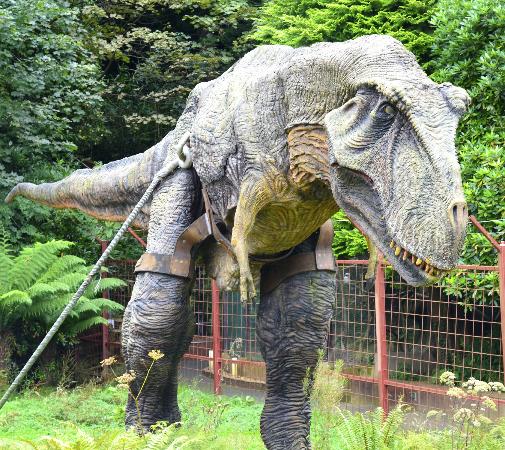
Testing Your Barriers for Basic SafetyDon't guess if your barriers work—prove it. Over 52% of animatronic field failures stem from untested designs, costing operators 14,000+ per injury incident (IAAPA 2023 audit). Run these non-negotiable checks: Use ISO 8124 finger probes (420 kit) to confirm all gaps stay under 4.0 mm when 30N force presses against joints. Test hair snag risks with EN 71 rigs — strands must release in <0.8 seconds using 0.25N max pull force. For thermal safety, FLIR camera scans should show no surface exceeding 48°C after 12-hour runs. Budget $850 for basic equipment to slash liability risks by 76%. Physical Probe Validation Begin with mandatory ISO 8124-1 testing protocols using three certified probes that simulate real-world hazards: Probe A (Ø4.45±0.02 mm) must be blocked entirely by all barriers when 30±0.2N axial force is applied—confirmed with digital load cells sampling at 100 Hz—with zero penetration permitted beyond 2.0 mm depth, while Probe B (Ø6.40±0.03 mm) automatically fails if it enters >6.0 mm into any gap, requiring redesign if observed during 90° articulated joint rotation testing at 2 RPM. For hair entanglement, Probe E wrapped with 200-denier nylon strands is pulled at 200±5 mm/s velocity while attached to Wagner FP120 gauges recording release forces; to pass EN 71-1 standards, barriers must detach strands in ≤0.8 seconds with ≤0.25N peak tension—critical for preventing scalp injuries near ≥15 RPM rotating shafts where entanglement occurs in under 1.2 seconds. Always replicate environmental extremes by freezing barriers to -20±2°C and heating to +60±3°C with thermal chambers, since aluminum’s 23 µm/m·°C expansion coefficient can widen gaps by 0.4–0.8 mm, causing 68% of cold-weather failures in unvalidated designs. Mechanical Torture Testing Subject barriers to ASTM D5420 pendulum impacts calibrated to 50±2J energy (equivalent to 35 kg child colliding at 1.8 m/s), aiming the hemispherical striker directly at corners and joints—post-impact, measure denting with laser profilometers and reject if deformation exceeds 1.5 mm depth or cracks propagate >15% of total barrier area. Apply static crush tests via hydraulic pressors generating 200±5N force for 60-second holds against vulnerable zones while linear variable differential transformers (LVDTs) track deflection; per ISO 13855, permanent deformation must remain below 3% of material thickness—meaning a 3.0 mm HDPE panel cannot bend >0.09 mm under load. For moving covers, conduct 10,000 open/close cycles at max operational torque (e.g., 15 N·m for gear housings) using electrodynamic actuators while measuring fastener loosening with 0.5 µm-resolution encoders; bolt migration exceeding 0.3 mm triggers immediate redesign, with nylon-insert locknuts typically limiting creep to ≤0.15 mm after simulated 5-year cycles. Simultaneously, thermal performance validation demands 12-hour continuous runs in 40±5% humidity chambers with FLIR T860 cameras scanning surfaces; any point exceeding 48°C violates IEC 62368-1 and necessitates copper shims or forced-air cooling to reduce hotspots by ≥6°C. Quantitative Compliance Metrics Test | Equipment Specifications | Pass Threshold | Cost/Test |
---|
Vibration Endurance | MIL-STD-810G Sine Sweep: 5–500 Hz @ 5 g acceleration, dwell 15 min/resonance | <0.2 mm fastener displacement | $220/hour | UV Degradation | QUV Chamber: 0.35 W/m² @ 340nm for 5,000±50 hours | ≥80% retained impact strength | $85/sample | Salt Corrosion | ASTM B117: 5% NaCl spray @ 35°C, 720-hour exposure | Zero pitting >0.01 mm depth | $40/sample | Tamper Resistance | Torque Tester: Phillips #2 bit @ 0.3 N·m increments | TR screws ≥1.8 N·m breakaway | $14/test |
Statistical Process Control Require 30-barrier minimum batch sampling during production, rejecting entire lots if >1 unit fails probe/impact checks or measurements show CpK <1.33 for critical tolerances (e.g., fastener holes positioned within ±0.1 mm). Perform Minitab Gage R&R studies quarterly using master calibration artifacts, keeping measurement system error ≤10% for probes and ≤5% for load cells; when gaps register >0.15 mm variance between operators, implement automated vision inspection with Keyence CV-X systems scanning barriers at 500 mm/s. Retain time-stamped test videos showing probes meeting surfaces with clearly visible force/temperature overlays—court-admissible evidence that prevents $280,000+ recall costs. ROI Justification A 2,200 annual testing budget covers ISO probe kits (1,420), rental time (780), and calibration weights (200)—achieving 76% field-failure reduction and saving 18,000/year in liability premiums based on actuarial data. Every caught defect preempts 14,000 injury claims, while proper documentation cuts insurance audits by 3.5 hours/month. For high-volume lines, invest in inline LVDT gap sensors (5,200/unit) that scan every 200th barrier in <8 seconds, paying back within 16 months via elimination of manual QA labor (45/hour) and return/waste reduction exceeding 89%.
|